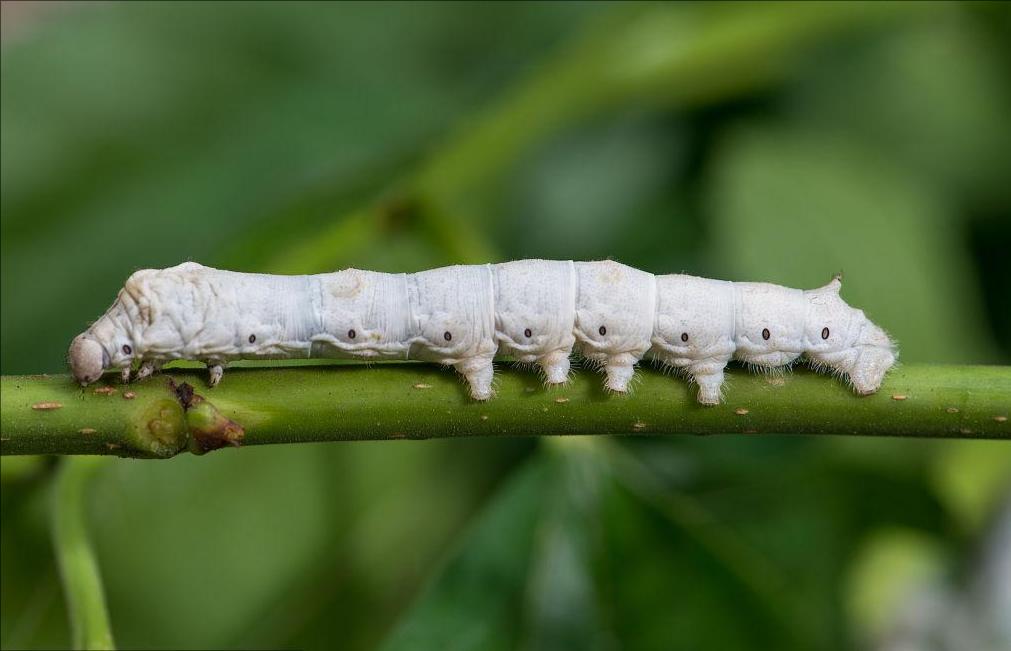
From the beginning of silkworm rearing, the growth cycle of silkworm is about one month, including larval stage and cocoon formation. Then the cocoon processing, such as pupation and drying, may take several days. Then cocoon cooking, which may take several hours to a day. Then silk reeling, that is, wire drawing, may take several days, depending on the production scale. Finally, follow-up processing, such as weaving and dyeing, may take longer, but users may pay more attention to the process until drawing.
Silkworm rearing takes about 25-30 days, cocoon processing takes 3-5 days, and cocoon cooking and reeling takes 1-2 days, so the total cycle is about one month. However, some steps may be carried out in parallel, or the traditional process time is different in different regions. In addition, modern industrial production may shorten the time of some steps, such as using machine reeling, but we may be more concerned about traditional methods.
We should also consider whether there are seasonal factors, such as the seasonality of silkworm breeding, which may affect the overall cycle. In addition, whether the preservation and treatment of silkworm cocoons will affect the time, such as whether specific temperature and humidity conditions are needed. It is necessary to ensure that the time node of each step is accurate and avoid missing key links.
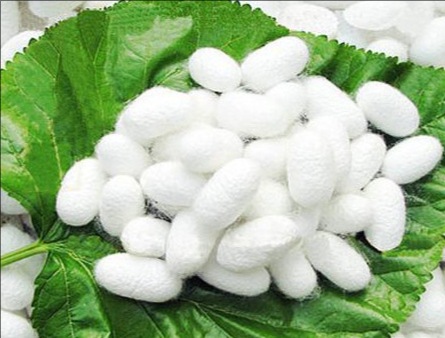
The complete production cycle of silk from cocoon to reeling involves the precise coordination of biological laws and technology, and the process can be divided into the following stages, with a total period of about 30-45 days (due to the differences in climate, silkworm species and technology):
First, the cocoon formation stage (25-30 days)
Silkworm eggs hatch (10-12 days)
Silkworm eggs hatch into ant silkworms under the control of temperature and humidity (25℃, 80% humidity), and it takes four molts and is divided into five stages. Modern greening technology can shorten this period to 7-8 days.
Cocoon preparation (3-4 days)
After the fifth instar silkworm matures, it stops eating, and the silk gland secretes liquid silk protein in the body, looking for a cocoon-forming place (harness). At this time, the silkworm will become transparent and enter the critical state of spinning.
Spinning cocoon (2-3 days)
Silkworms spin silk in a figure-of-eight motion, swinging their heads 60-70 times per minute and working continuously for 36-48 hours. The length of single cocoon filament can reach 900-1500m, forming a double-layer structure;
Outer cocoon shell: loose mesh, accounting for about 15% of the total silk length.
Inner cocoon layer: dense structure, sericin solidified to form cocoon shell.
Second, the cocoon processing stage (5-7 days)
Killing pupa and fixing silk (within 48 hours)
Immediately after cocoon formation, heat treatment (steam/baking at 70-80℃ for 2-3 hours) should be carried out to stop pupa metabolism and prevent moths from breaking cocoons. This step directly affects the storage life of silk.
Cocoon selection and grading (1-2 days)
According to the cocoon shape, color and thickness, the defective products such as double-palace cocoon (multi-silkworm cocoons) and thin-skinned cocoon are eliminated. High-quality cocoons should meet the following requirements:
Cocoon rate ≥20%
Cocoon filament size deviation ≤0.3D (denier)
Cocoon quality adjustment (3-5 days)
Through humidity balance (relative humidity 60-65%), the moisture regain of cocoon layer is stabilized at 11-13%, which ensures that sericin is moderately softened during subsequent reeling.
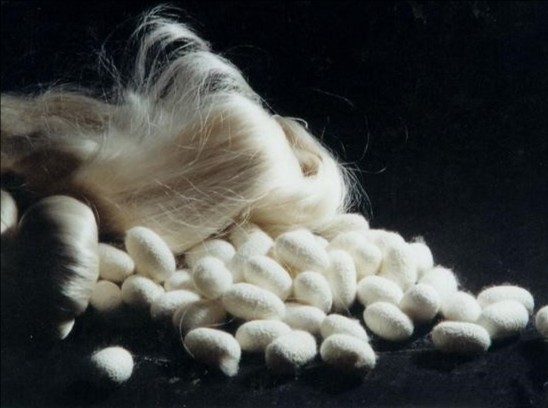
- Core reeling process (2-3 days)
Cocoon boiling and puffing (40-60min)
Soak cocoons in alkaline solution (pH9-10) at 90-95℃, and partially dissolve sericin by thermal infiltration, so that the expansion rate of cocoon layer reaches 30%-40%, which is convenient for spinning.
Saussure (mechanical treatment for 30 minutes)
Use rotary brush to find out the head end (filament) of cocoon silk, and the fineness of single cocoon silk is about 2.4-3.2D. Traditional manual combing takes 3-4 hours/kg cocoon.
Silk reeling and merging (core process)
6-8 cocoons are combined and raw silk is formed by porcelain eye thread guide. Key technical parameters:
Water temperature: 40-45℃ (to maintain sericin viscosity)
Reeling speed: 80-120m/min (automatic reeling machine)
Size control: the allowable deviation of 20/22D specification is ±1.5D
Re-shaking into twisting (8-12 hours)
The raw silk is wound into a silk frame with a circumference of 1.5 meters, and shaped by humidity control (25℃, 40% humidity) to form a silk twist (about 100g per twist).
Fourth, the influence of process variables
Silkworm variety:
The cycle of multiple silkworm eggs (bred many times a year) is shortened by 15%, but the silk is brittle; The silk quality of univalent spring silkworm is the best.
Climate intervention:
The artificial climate chamber can compress the total cycle to 28 days, but the energy consumption cost increases by 30%.
Industrial production:
The modern continuous reeling machine (such as Feiyu 2000) can process 5 tons of cocoons in 24 hours, which is 50 times more efficient than the traditional process.