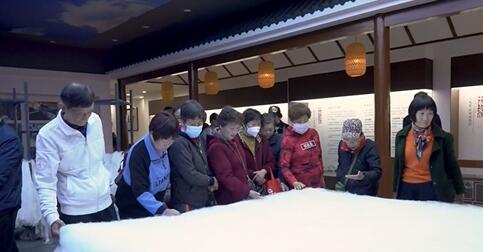
First, I need to determine the user’s demand level. Do they just need a basic step overview or a more detailed process explanation? Considering that the previous answers are detailed, users may want a comprehensive production process, including traditional and modern methods.
Next, I have to recall the main steps of silk making. Silkworm rearing, cocoon harvesting, reeling, weaving, refining, dyeing and finishing. Each step needs to be briefly explained, and some key technical points may need to be mentioned, such as the temperature control of reeling or the application of modern machinery.
Also pay attention to the possible deep needs of users. For example, they may be interested in the difference between traditional hand-made and modern industrial production, or want to know why silk is precious and whether it is related to the complexity of the production process. Therefore, in the answer, it is necessary to emphasize the contrast between manual and mechanical, as well as the fineness of each step.
In addition, the user’s previous questions involve different cultures and history, and there may be cultural or historical elements in the silk making process, which can be mentioned appropriately. For example, the differences between China’s traditional silk reeling technology and Japan and Europe, or the historical evolution of some steps.
You need to avoid using overly technical terms, but be accurate. For example, when explaining “reeling”, it can be simplified as “drawing silkworm cocoons into silk threads”, and it is mentioned that silkworm cocoons need to be treated with hot water to dissolve sericin. This is both easy to understand and accurate.
Also consider whether the structure of the answer is clear. Step by step, organized with titles and lists, making it easy for readers to follow the process. It may be divided into several major steps, each of which has sub-points, such as sericulture, cocoon harvesting, reeling, weaving, refining, dyeing and finishing, and each part is explained in detail.
Finally, check whether there are any missing important links. For example, the selection of silkworm varieties, the quality classification of silkworm cocoons, or the post-processing technology of silk, whether these need to be mentioned in the answer. Ensure that the whole process from silkworm to finished product is covered, and highlight key technologies and technological difficulties.
To sum up, users need a comprehensive, clear structure, traditional and modern silk production process, and explain the importance and technical details of each step, and may also want to know the cultural and historical background. Ensure that the answers are both professional and easy to understand, and meet the knowledge needs of users.
The production of silk is a complex process that combines natural ecology, handicraft skills and modern science and technology. Its core lies in extracting silk fibers from silkworm cocoons and processing them into fabrics. The whole process can be divided into four stages: sericulture, cocoon collection, reeling, weaving, refining and finishing. The following is the detailed flow:
First, sericulture and cocoon harvesting: the weaving starting point of life
Silkworm egg cultivation
Selecting high-quality silkworm eggs (such as Bombyx mori) needs to be hatched in a constant temperature and humidity environment. Young silkworms feed on fresh mulberry leaves and undergo molting for 4 times (about 25-30 days) until they mature at the fifth instar.
Cocoon into silk
Mature silkworms stop eating and look for a dry scaffold to spin silk and cocoon. Silk is made of two monofilaments (mainly silk fibroin) bonded by sericin, and the length of a single cocoon filament can reach 800-1500m.
Key control: temperature (20-25℃), humidity (60-70%) and ventilation to ensure the cocoon quality is uniform.
Cocoon harvesting and sorting
7-10 days after cocoon formation, silkworm cocoons should be picked manually before pupation, and classified according to size, color and integrity. High-quality cocoons are used for reeling, and secondary cocoons are processed into silk spinning raw materials.
Second, reeling: the transformation from cocoon to silk
Killing pupae and cooking cocoons
Killing pupae: by drying (traditional exposure to sunlight, modern steam or hot air), silkworm pupae are prevented from breaking cocoons and damaging silk fibers.
Cocoon boiling: Soak the cocoon in 90℃ alkaline solution (such as soapy water or sodium carbonate), dissolve part of sericin, and soften the cocoon layer for spinning.
Spinning and twining
Manual Silk Reeling: Combine several cocoon filaments (usually 5-10) with a wooden reeling car, and adjust the reeling speed by sensing the thickness of the filaments with your fingers.
Mechanical Silk Reeling: Modern automatic silk reeling machines cluster multiple cocoon filaments by rotating porcelain eyes to form raw silk with uniform thickness (20/22 denier is a common specification).
Winding and drying
Raw silk is wound into hank or cheese, which is dried and shaped to become weaving raw materials. In the traditional process, the sericin of raw silk is light yellow; After refining, sericin is removed and white luster appears.
Third, weaving: the artistic reconstruction of silk thread
Preparatory process
Winding: Reewinding the skein yarn to the bobbin to remove impurities and broken ends.
Twinning: according to the design requirements, multiple raw filaments are combined and twisted to enhance strength or create texture (such as strong twisting process of crepe).
Warping: hundreds of silk threads are arranged in parallel at a fixed tension and wound on the warp beam to provide warp threads for the loom.
Weaving technology
Traditional hand loom:
For example, China Yunjin’s “Big Flower Building Wood Machine” needs two people to cooperate, one person jacquard and the other person shuttles, and only weaves 5-6 cm a day.
Japan West Array Weaving uses an “empty loom” to control complex patterns with paper patterns.
Modern shuttleless loom: water jet and rapier loom can realize high-speed automation, and can weave high-density satin and jacquard fabrics.
Typical silk category
Plain fabrics: spun silk, electric spinning (plain weave) and crepe de chine (strong twist crepe).
Floral fabric: brocade (colorful jacquard), velvet (cut velvet) and nylon (twisted warp through holes).
Fourth, refining and finishing: giving silk soul.
Refining degumming
Soak raw silk fabric in enzyme-containing or weak alkaline solution (pH 9-10) and cook at 95℃ for 2-4 hours to remove residual sericin (accounting for about 25% of raw silk weight) and release silky luster of silk.
Dyeing and printing
Plant dyeing: traditionally, madder (red), bluegrass (indigo) and sappan (purple) are used, and mordant fixation is needed.
Modern technology: acid dyes (suitable for silk protein) and digital printing accurately restore complex patterns.
Characteristic techniques: China’s “silk reeling” warping and weft breaking, and Indonesian Batik dyeing prevention.
afterfinish
Weight gain treatment: immersion in tin salt solution increases the drape of fabric (but it is easy to age and is gradually eliminated in modern times).
Sand washing: silk is slightly raised with alkaline solution, showing an old-fashioned texture.
Anti-crease finishing: epoxy resin coating improves the wrinkle-prone characteristics of silk and adapts to the needs of modern clothing.
V. Modern technology and innovation
Silkworm rearing with artificial feed: break through the dependence on mulberry leaves and realize industrialized farming.
Transgenic silk: implanted with spider silk gene to improve strength, used for medical suture.
Environmental protection technology: waterless dyeing technology and sericin recycling to reduce pollution.
Conclusion: The Contemporary Echo of Millennium Craft
From the rustling sound of silkworm babies eating mulberry leaves to the rhythm of loom shuttle, silk making is an epic of cooperation between human beings and nature. Every silk is condensed with biological miracle, craftsman’s wisdom and chemical research, and its process is both technical inheritance and aesthetic pursuit. Nowadays, this ancient skill is being reborn in the fields of medical care, environmental protection and high-end fashion through scientific and technological innovation.